Green building blocks for green chemistry
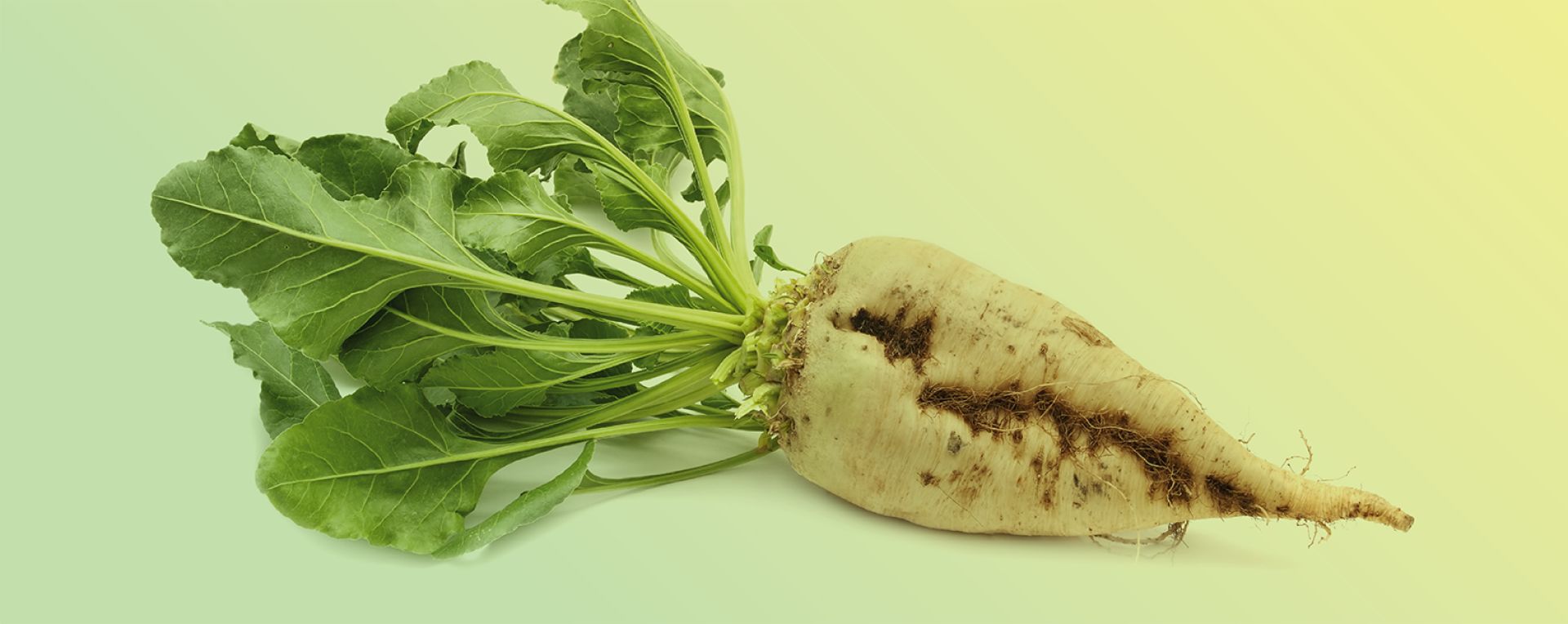
Wherever you look, you can’t fail to see the results of the chemical industry. Our children’s plastic building blocks, our medicines, our food, and the plastic packaging that keeps them fresh for longer. It's almost impossible to imagine modern life without products from the chemical industry. But the main constituents of these everyday products must become greener and more sustainable. According to scientists, that's within our reach. Here's a look into the future of green chemical building blocks.
SUSTAINABLE CHEMISTRYTime for an oil change: Chemport Europe is developing new green building blocks
Building the chemical industry of the future
Plastic drink bottles, LEGO bricks and mattresses – they’re all petroleum-based. Of every 20 products manufactured worldwide, 19 depend on the chemical industry. And since we all learned at school that the chemical industry can’t do without fossil resources, it will come as no surprise that chemical companies and liquid fuels together are responsible for a quarter of all CO2 emissions. That’s just the way it is.
Time for an oil change
Will the chemical industry remain petroleum-dependent? That is no longer the case. New technological developments have long been underway to make plastic bottles, LEGO bricks or mattresses from sugars or lactic acid, for example. Some synthetic materials can even be made using greenhouse gases as a raw material. Environmentally friendly bio-based monomers are already the base material for various plastics used by manufacturers of cars, aircraft, toys, computers and mobile phones. Some technologies are already in use, others are still under development. So however much you see the chemical sector as a problem, it’s also the solution. Thanks to the chemical industry, we now have batteries for green energy storage and electric cars. If the basic building blocks of chemistry themselves are made more sustainable, it won’t be long before the world becomes much more environmentally friendly.
Chemistry: the green motor
And about time. Everybody working within the chemical industry is convinced that it urgently needs to become more sustainable. It has to work with green building blocks in order to achieve the objective of the Paris Agreements. There’s still a long way to go with that. Technology alone is not enough. For oil-based products, processes have been optimised after decades of building and development. The entire infrastructure is prepared to carry on producing petroleum-based plastics. Pioneers in sustainable chemistry face a major challenge in building this infrastructure from scratch. In the Netherlands, the TopDutch region is at the forefront of this. The chemical cluster in the northern part of the Netherlands, Chemport Europe, aspires to become the world’s first CO2 negative production location by 2050. But how? And where can you connect as an entrepreneur in the chemical industry? These are chemistry’s three most important new green building blocks, and how they are given shape in the TopDutch region.
Biomass: Agriculture and industry in one product stream
The challenge: accelerating biobased chemistry
The first new raw material is biomass. Crops and residual streams from agriculture and the food industry are potential sources of chemicals, materials, fuels and energy. A truly biobased economy is being created as more and more technologies for converting this raw material are developed. Biomass is also expected to replace the role of oil and other fossil fuels in chemistry.
Fun fact: fossil fuels are actually derived from biomass that was hidden under thick layers of earth ages ago. But could it be possible to speed up this process of millions of years, in order for an industry to emerge from it? That is one of the challenges. Another is to make the extraction of chemical building blocks from biomass renewable. For example, energy can be obtained by burning biomass, but this results in the emission of large quantities of particulate matter. Therefore, it is better to use biomass as a resource for the production of building blocks for bio-based plastics.
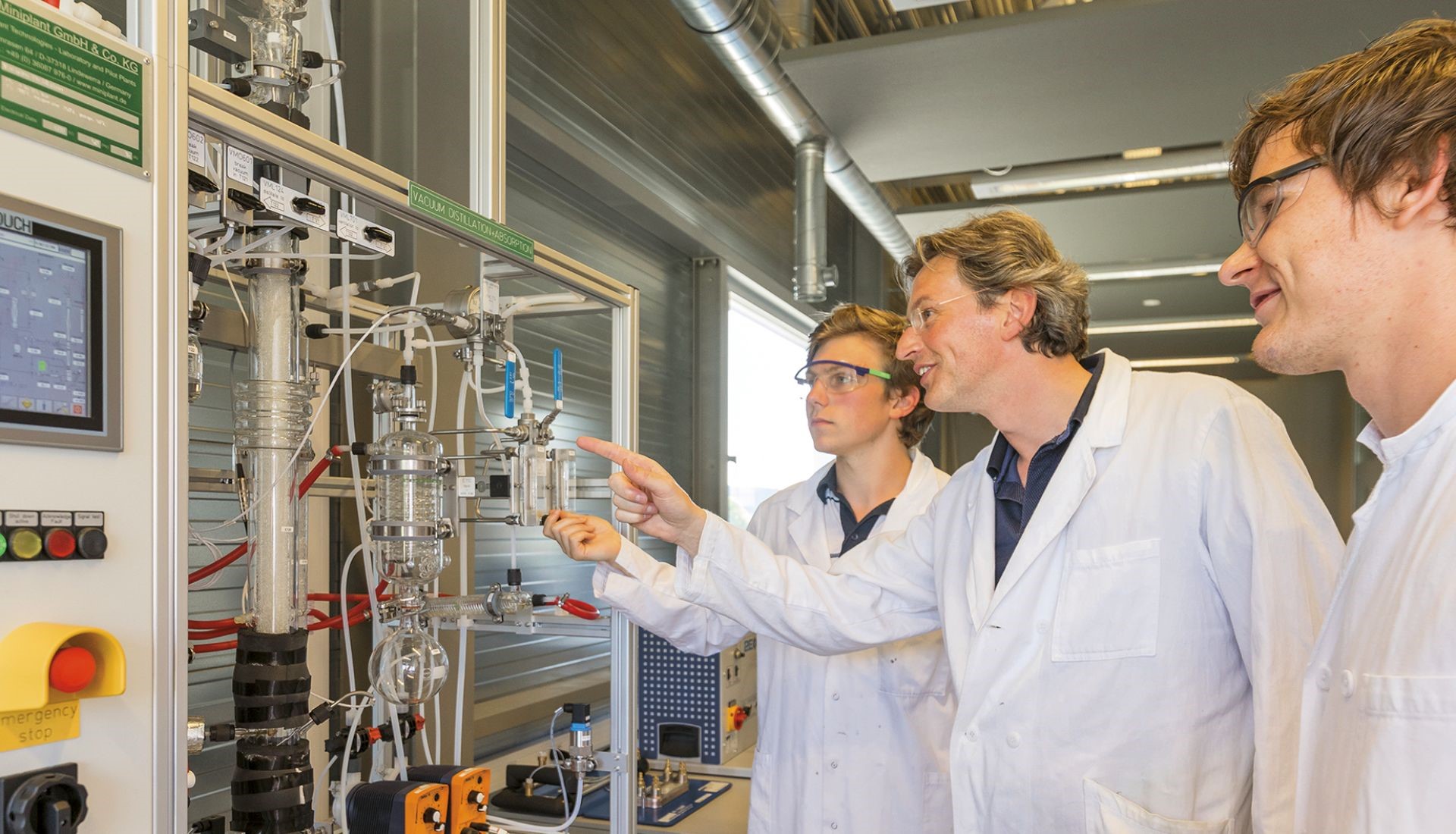
Renewable raw material extraction from biomass - what does this call for?
A developed agricultural hinterland
First of all, an agricultural hinterland. With a large agricultural area and the highest production per hectare in Europe, the Netherlands is assured of a supply of biomass. In the Northern Netherlands there are excellent train, road and water connections between the agricultural hinterland and the chemical cluster. These are residual streams of potatoes, sugar beet, grain, rapeseed, maize and even wood and grass, from which scientists are able to extract useful raw materials. These residual flows are used to generate carbohydrates, proteins, sugars and fibers, which are converted into semi-finished products via biorefinery. For example, a research team led by Gert-Jan Euverink, professor of Biotechnology at the University of Groningen, the Netherlands, is conducting research into shrimp shells. Until recently they ended up en masse on the waste mountain. According to Euverink, that’s a pity: there’s much to be extracted from this biomass. ‘These shells contain chitin, a component that can be transformed into the substance chitosan, a carbohydrate with antibacterial properties. It could be used for wound sutures, for instance. We’re also thinking of antifouling for ships, where chitosan prevents barely any algae from growing, if at all.’ Euverink’s research is based at the laboratories of Zernike Advanced Processing (ZAP) in Groningen. Companies can test new technologies together with students and PhD students at this research center on the university campus. Euverink describes this as an important link between science and business. ‘A technology that has proven itself in the lab can be tested here on a larger scale. We’re looking into how best to extract a few kilos of raw materials from a particular crop or food waste.’
A technology that has proven itself in the lab can be tested here on a larger scale. We're looking into how best to extract a few kilos of raw materials from a particular crop or food waste.
Prof. dr. G.W.J. (Gert-Jan) Euverink
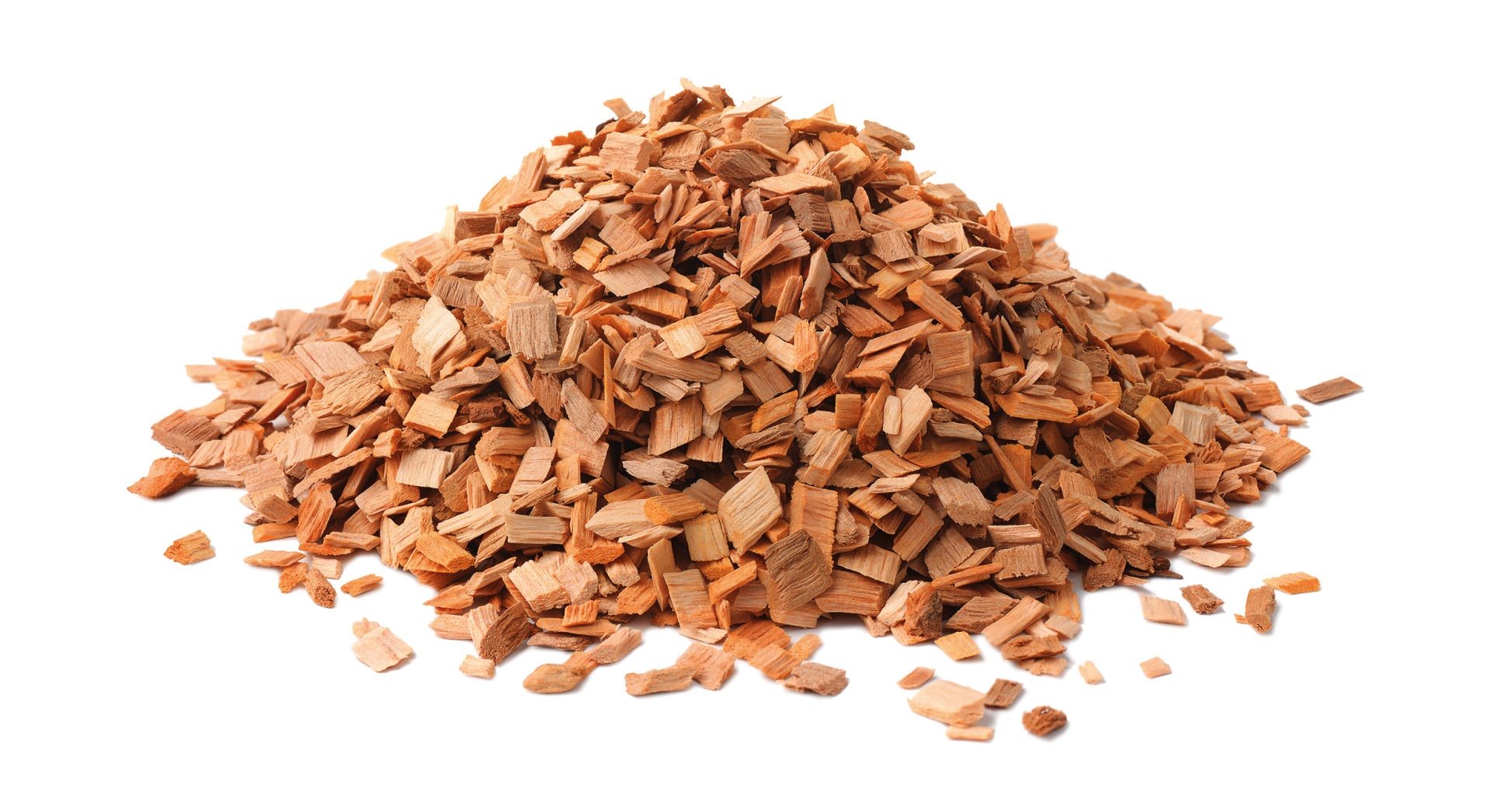
Forests for woodchips
Biorefinery plants are essential for a biobased economy, explains Professor Euverink. ‘As many high-quality products as possible are extracted from biomass at plants such as these. Unlike petrochemicals, this is done at low temperatures and under low pressure, and the procedure is often based on water. The advantage of this is that the various streams remain better usable. In chemical processes at high temperatures, many molecules are so severely damaged that they can no longer be used.’ A big step forward will be taken in 2019. This year, a test plant is due to open to extract glucose from wood chips at the Chemport Industry Campus, a test area in the Northern Netherlands chemical complex. Technology company Avantium is the initiator of this biorefinery. A commercially exploitable plant, that is yet to be built, will be used to convert woodchips from the Province of Drenthe and Groningen’s publicly-managed forests into chemical raw materials such as sugars, glucose and lignin.
Unlike petrochemicals, this is done at low temperatures and under low pressure, and the procedure is often based on water. The advantage of this is that the various streams remain better usable. In chemical processes at high temperatures, many molecules are so severely damaged that they can no longer be used.
Prof. dr. G.W.J. (Gert-Jan) Euverink
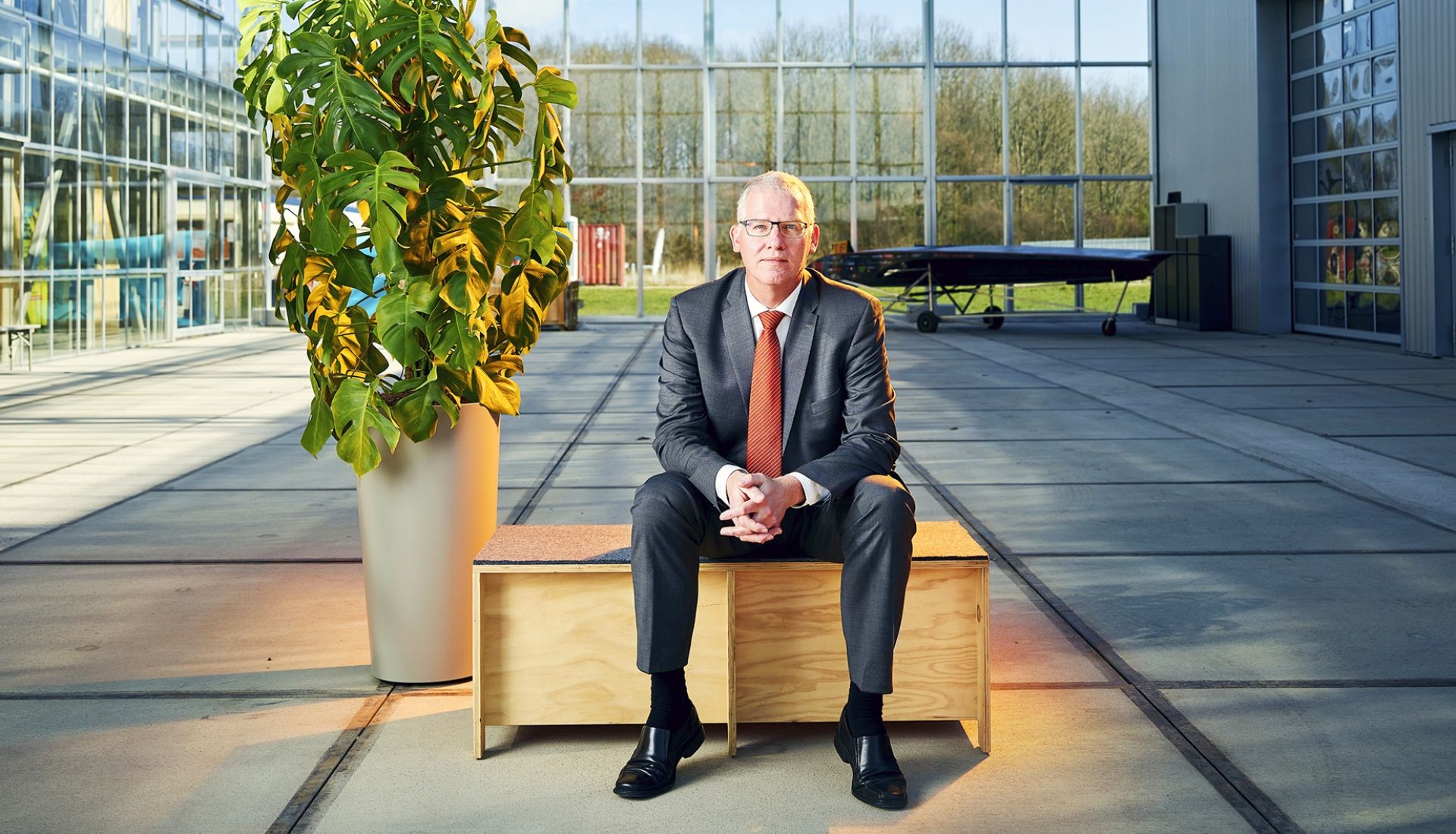
The sugars obtained from the Avantium biorefinery, for example, could go to the neighboring Nouryon, the former AkzoNobel Specialty Chemicals. Those sugars could subsequently be used to produce acetic acid, a product currently made with fossil resources. The other raw material, lignin, is also a valuable material. What remains of the woodchips ends up as biomass in the RWE power plant. ‘The arrival of the Avantium biorefinery is a major breakthrough’, says Euverink, who expects more biorefinery plants to emerge in the coming years.
The ambition: scaling up biobased chemistry
The technologies for extracting raw materials from woodchips and shrimp shells have already been tried and tested. But the biggest challenge is to scale up the technology. ‘A desirable chemical reaction in a test tube is not easy to reproduce on an industrial scale in new technology’, says professor Euverink. The Dutch chemical sector estimates that by 2030 about 15 percent of the raw materials will be extracted from biomass. That percentage is three times higher than it is now. Chemport Europe, with its sustainable ambition, will take on a leading role in this transition.
Carbon dioxide: From greenhouse gases to industrial resource
The challenge: CO2 from emission to input
But as biomass-based production increases, the biggest problem has yet to be addressed: carbon dioxide. The fact is that industry emits greenhouse gases. But what if it were possible to use CO2 as a raw material for the chemical industry? That would be a win-win situation: thanks to industry, undesirable quantities of greenhouse gases are reduced to an acceptable level and the industry itself emits less. Making this possible is the holy grail for scientists. Some even believe that this is the only way to achieve the agreed CO2 reduction of 80 percent by 2050 compared to 1990.
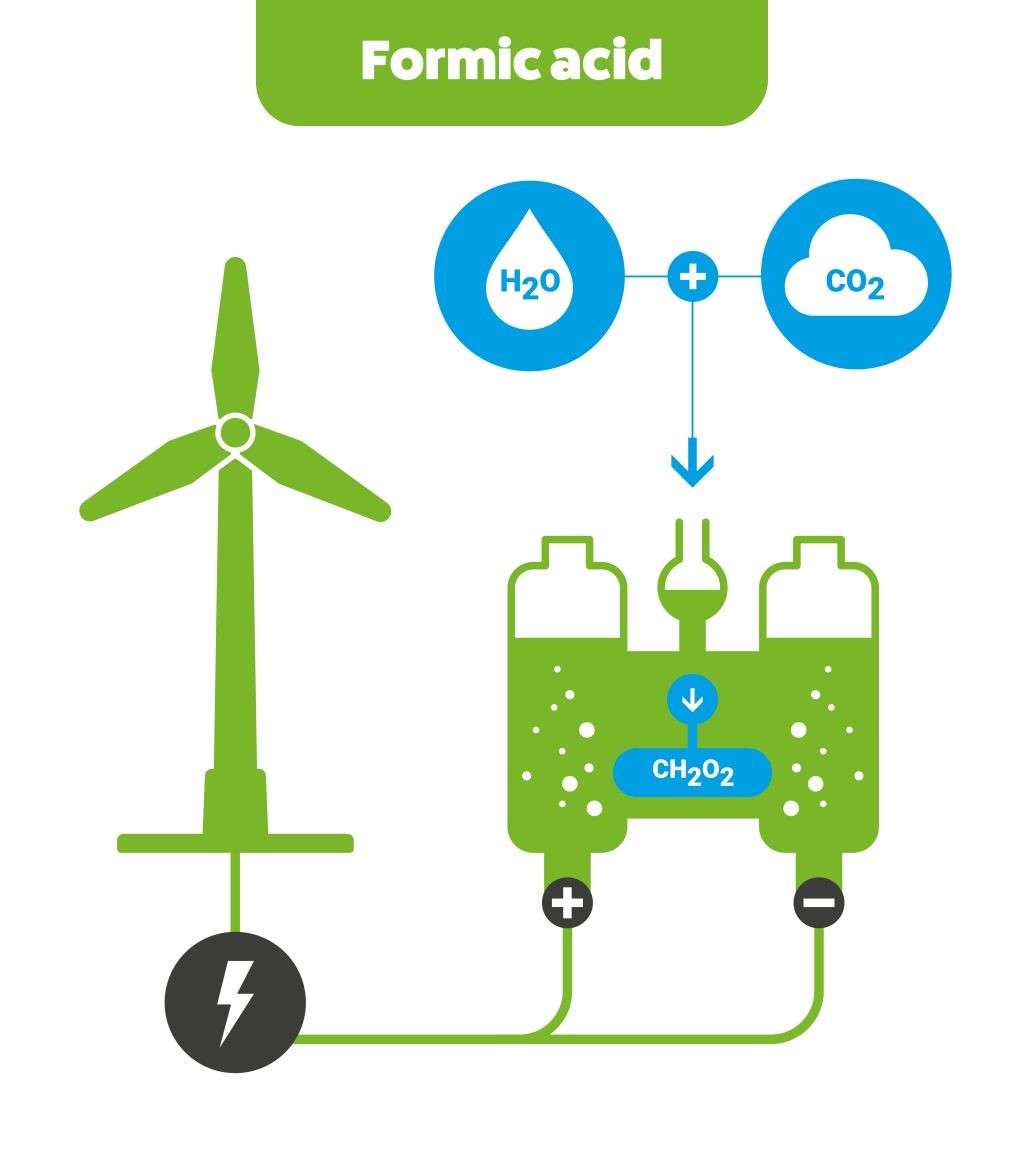
The ambition: develop the first CO2 negative chemical cluster
That’s why Chemport Europe aims to become the world’s first CO2 negative production location by 2050. But how? The technology to turn CO2 into a raw material for the chemical industry is still under development. Various scientists in the Netherlands are looking into the possibilities. It’s difficult to chemically split CO2, says Gert-Jan Gruter, endowed professor of Industrial Sustainable Chemistry at the University of Amsterdam. ‘The molecule CO2 is the chemical industry’s drain. It takes a lot of energy to turn it into a usable new raw material.’ A much more promising way is to use electricity: with hydrogen, you can convert CO2 into formic acid, for example. ‘That is a very useful building block for the chemical industry: formic acid can even be used as car fuel’, says Gruter, who is also Chief Technology Officer at Avantium. Gruter is not in favor of underground CO2 storage. ‘Carbon Capture and Storage (CCS) is a bad idea because it’s not a structural solution to the problem. It’s a modern-day landfill, that costs a lot of money and does not yield anything.’
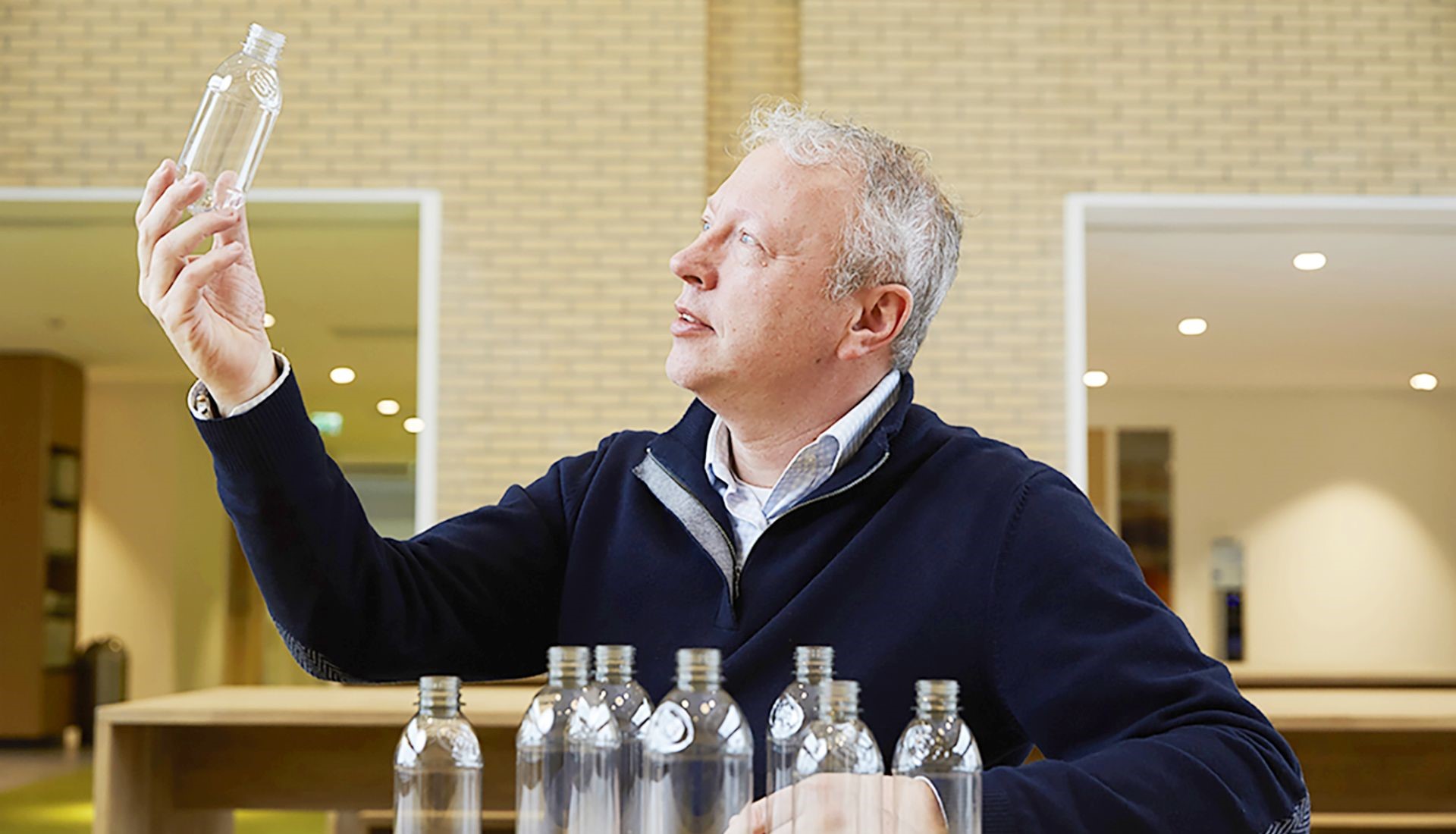
CO2: raw material for polymers and polyesters
Avantium is currently researching the best and most efficient technology for transforming CO2. A few years ago it took over the American startup Liquid Light. That company had mastered the technology, but had problems with scaling up and went bankrupt. Avantium acquired the patents and brought the equipment and staff to Amsterdam. Avantium’s laboratory now employs a research group of 15 people whose task includes continuing to develop the technology and ultimately scaling it up into a pilot plant. The Amsterdam-based technology company converts CO2 into formic acid using a catalyst and electricity. This liquid is subsequently reconnected to CO2 to form oxalic acid, a potential monomer for polymers and polyesters. Professor Gruter states: ‘There’s another chemical process that we can use to turn oxalic acid into glycolic acid, which serves as a raw material for specific types of suturing material. These substances dissolve naturally after two weeks.’
Carbon Capture and Storage (CCS) is a bad idea because it's not a structural solution to the problem. It's a modern-day landfill, that costs a lot of money and does not yield anything.
Prof. dr. G.J.M. (Gert-Jan) Gruter
Avantium has made a conscious choice not to focus on the production of fuels because raw materials for plastics have a better earning model. In the future, CO2 in particular may well become lucrative as a raw material for chemical building blocks. ‘The switch to renewable energy not only reduces electricity costs. If producers have to pay for their CO2 emissions, we’ll also earn from supplying this raw material’, according to the CTO. He believes that it remains a technical challenge to capture CO2. ‘These technologies are also still in their infancy, but it’s just a matter of time. On a global scale, a great deal of research is being done in this area.’
The switch to renewable energy not only reduces electricity costs. If producers have to pay for their CO2 emissions, we'll also earn from supplying this raw material.
Prof. dr. G.J.M. (Gert-Jan) Gruter
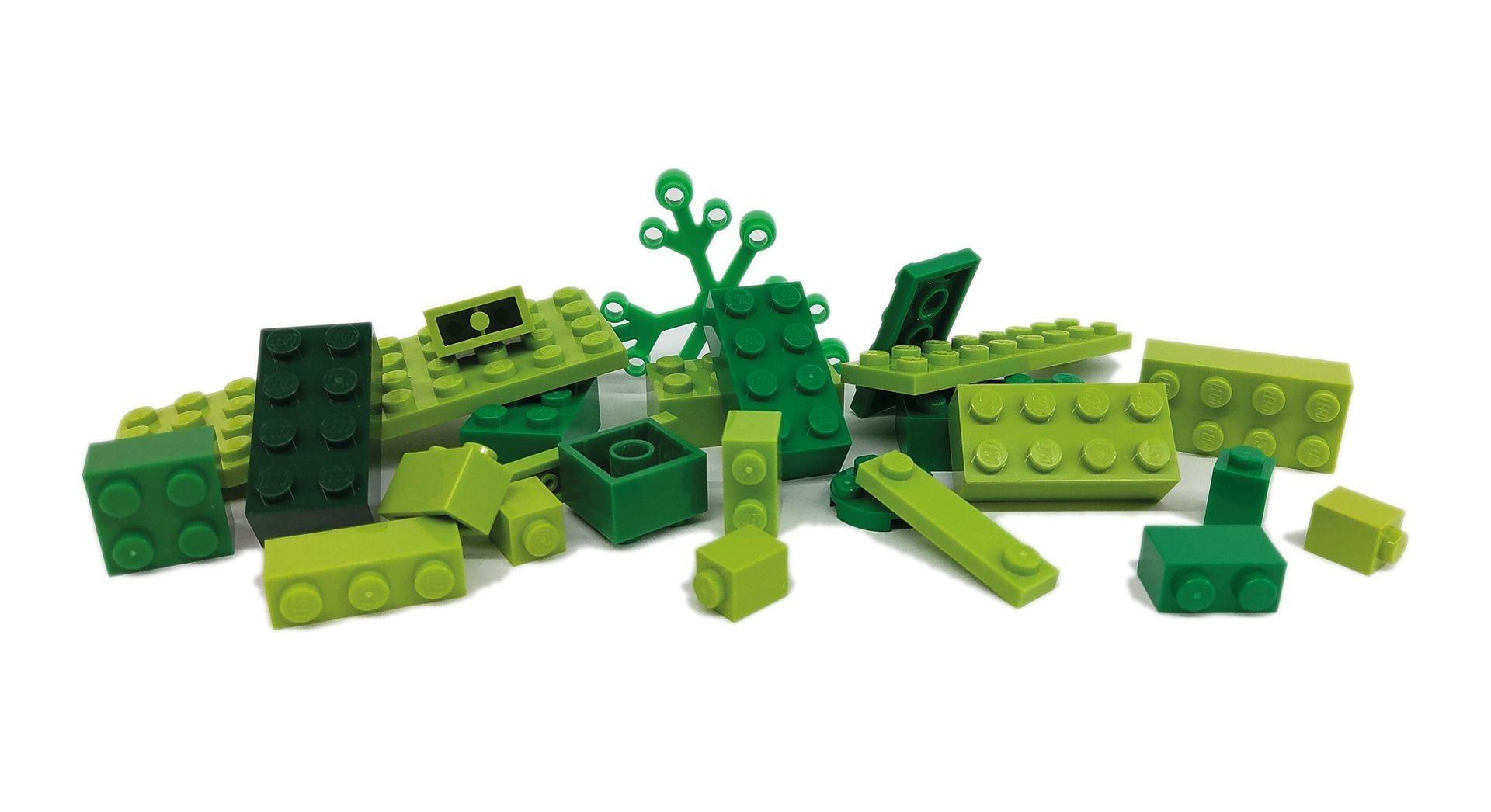
CO2: raw material for PET bottles and LEGO bricks
Professor Gruter is also conducting research into oxalic acid with colleagues at the University of Amsterdam. The research group Industrial Sustainable Chemistry (ISC) is conducting research together with toy manufacturer LEGO. They’re looking for a way of making the plastic building blocks from CO2 and biomass in the future. ‘We want to make high quality plastics that we can use to make even better plastic bottles in the future. We hope to be able to make a bottle that no longer needs to be melted down after recycling, but can be refilled after a thorough wash, just as we do with glass beer bottles.’ According to the professor, the chemical industry still has many opportunities to achieve a greener society. ‘The time has come to once again unravel all the elements of the periodic table.’
The time has come to once again unravel all the elements of the periodic table.
Prof. dr. G.J.M. (Gert-Jan) Gruter
CO2: raw material for cosmetics
At Chemport Europe, the young scale-up Photanol is also innovating with CO2 as a raw material. The company produces various organic acids from cyanobacteria, solar energy and carbon dioxide, which form the basis for the production of bioplastics and cosmetics. In 2019, construction is due to start on a pilot plant in Delfzijl (province of Groningen), which will source its CO2 from the neighboring Nouryon plant.
Hydrogen from gray to green
The challenge: a global hydrogen economy
And then we have a third green building block: hydrogen. In Japan, it is seen as the ingredient for a sustainable society. Japan is leading the way in the use of this renewable energy source, during the 2020 Olympic Games in Tokyo, the whole world will experience this. The Olympic village where more than 17,000 athletes and guests are staying will be transformed into a ‘hydrogen city’. All accommodation, sports locations and catering establishments will be supplied with electricity and hot water via hydrogen energy. Japan also aims to have around 35 hydrogen filling stations during the Olympic Games. The car brands Toyota and Honda are striving to put at least 6,000 hydrogen cars on the road.
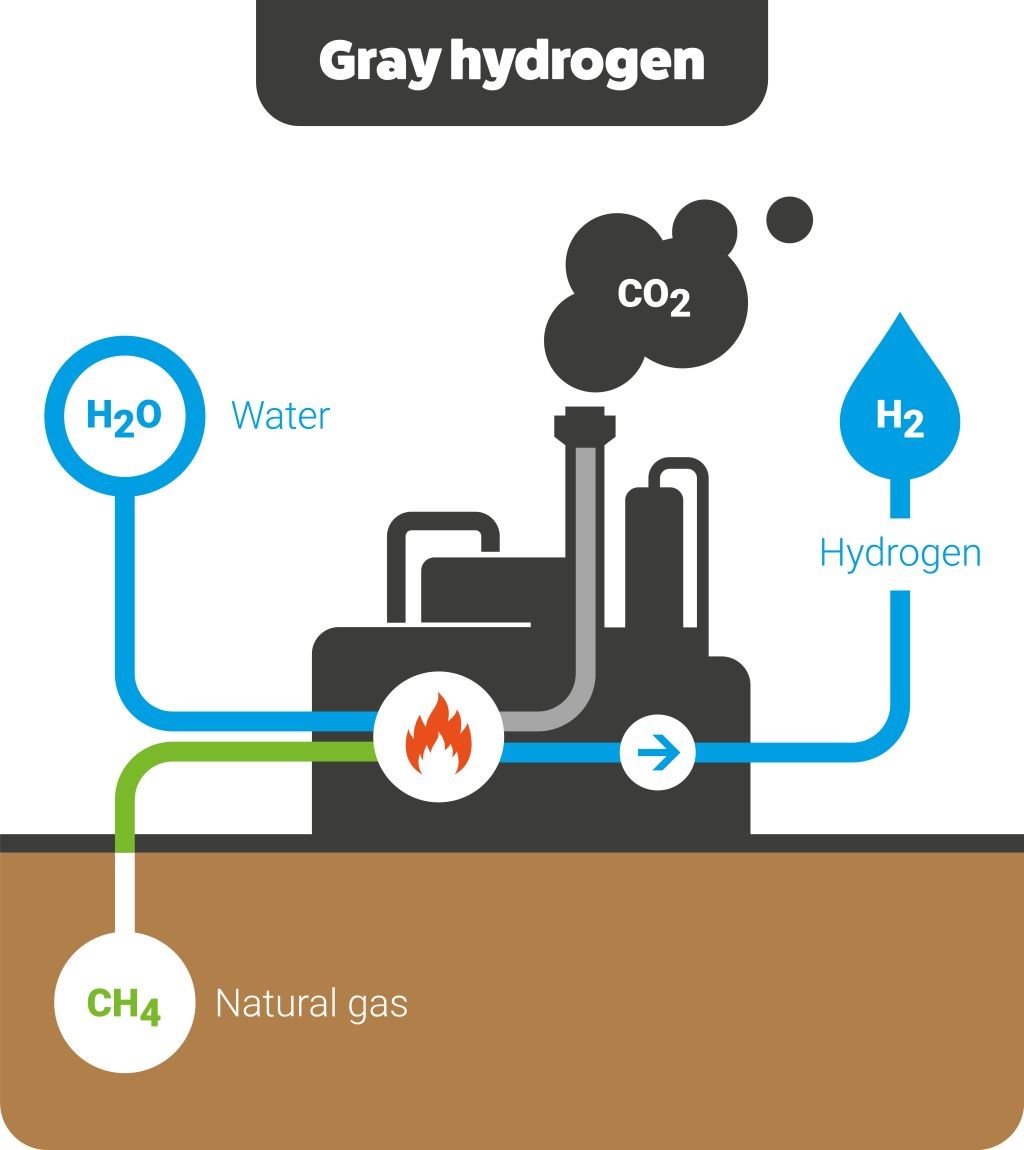
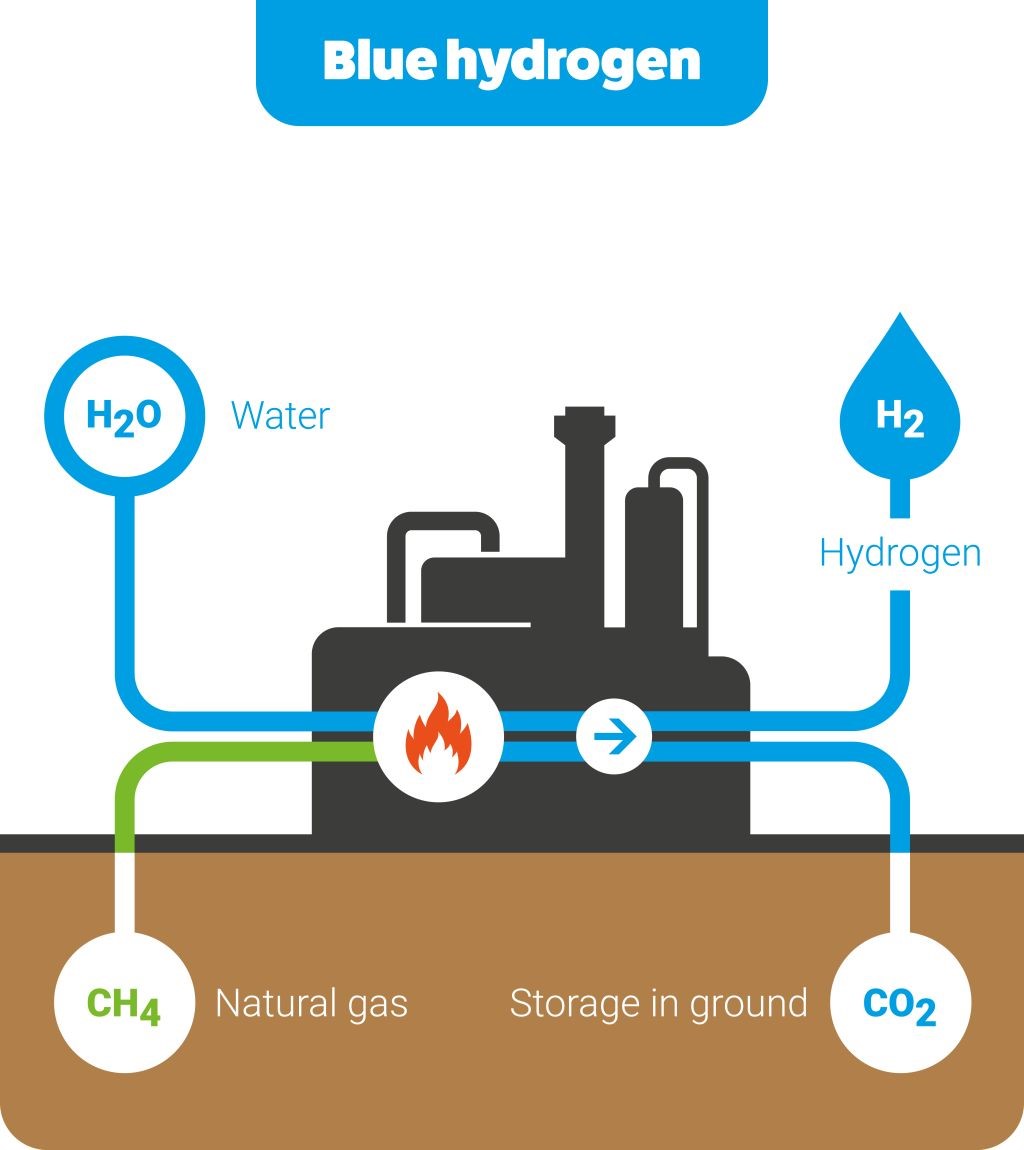
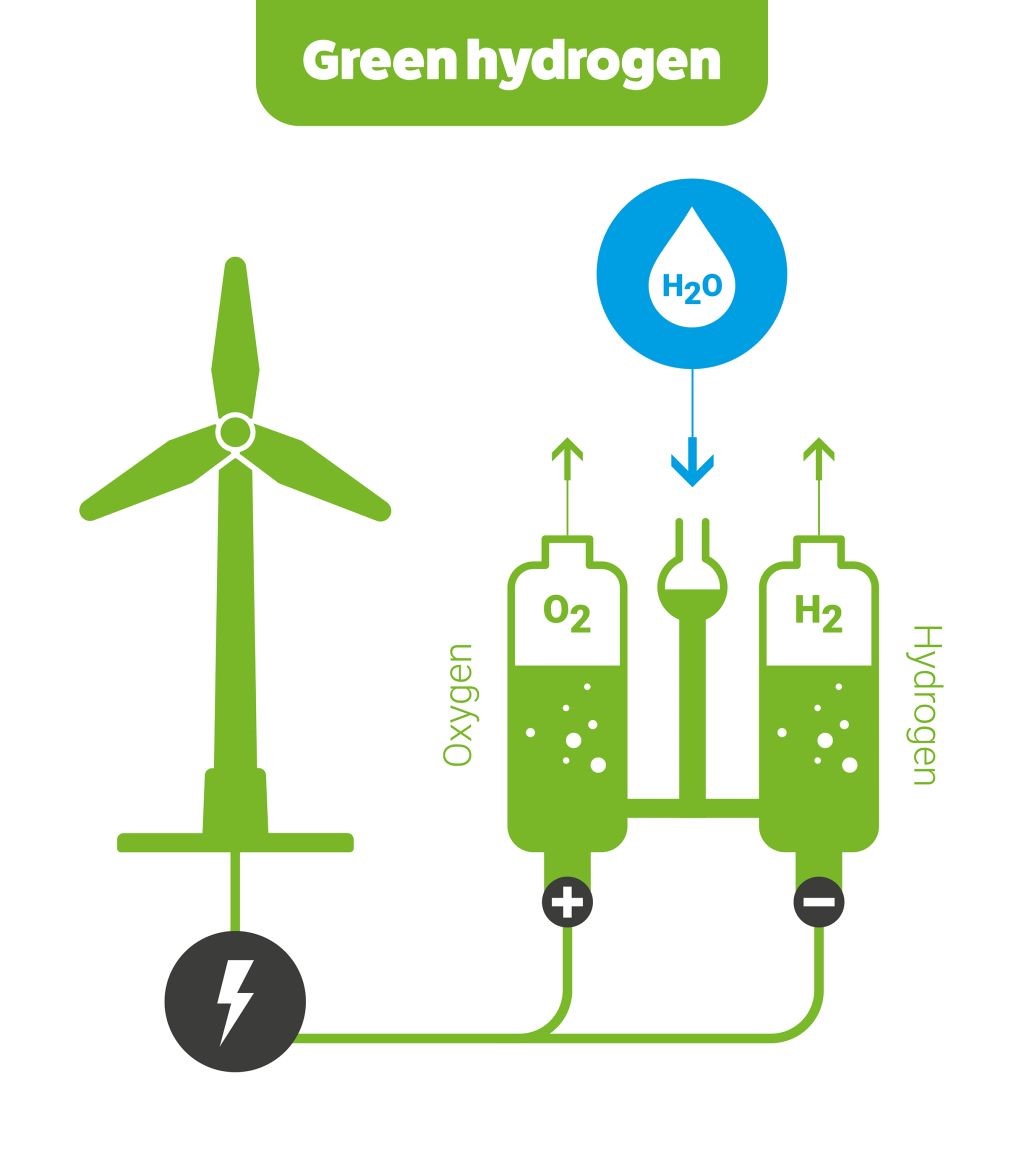
The Japanese government has been investing in large-scale projects to transform the country into a hydrogen-based society since 2014. For the time being, the country is extracting the hydrogen from Australian lignite. The hydrogen is to be extracted from fossil-free energy by 2040. The Japanese aren’t doing this for nothing. Green hydrogen not only serves as an environmentally friendly and safe fuel; it is also a useful building block for the chemical industry. Green hydrogen can be produced from green electricity through electrolysis. It can also be produced from biomass and biogases. This calls for gasification and steam reforming respectively. And the best thing about it: hydrogen can be transported through gas pipelines.
Dutch hydrogen economy: expertise, infrastructure and ambition
The Netherlands is also a strong advocate of hydrogen, which appears to present a solution to many problems. For example, the gas can be used to store sustainably generated energy, as large surpluses of wind and solar energy will become available in the future. The green energy can easily be converted into hydrogen, and - at a later stage or at another location - can just as easily be converted into green electricity. Hydrogen can also be used as a fuel for transport. But especially for the chemical sector, hydrogen is an important green building block. It is not only an alternative to natural gas and oil to run chemical processes, but can also be used as a raw material. The Netherlands does not yet have a large-scale hydrogen supply. Hydrogen is already being produced, as a residual stream from various chemical processes. But this is ‘gray’ hydrogen, because it is obtained from fossil natural gas.
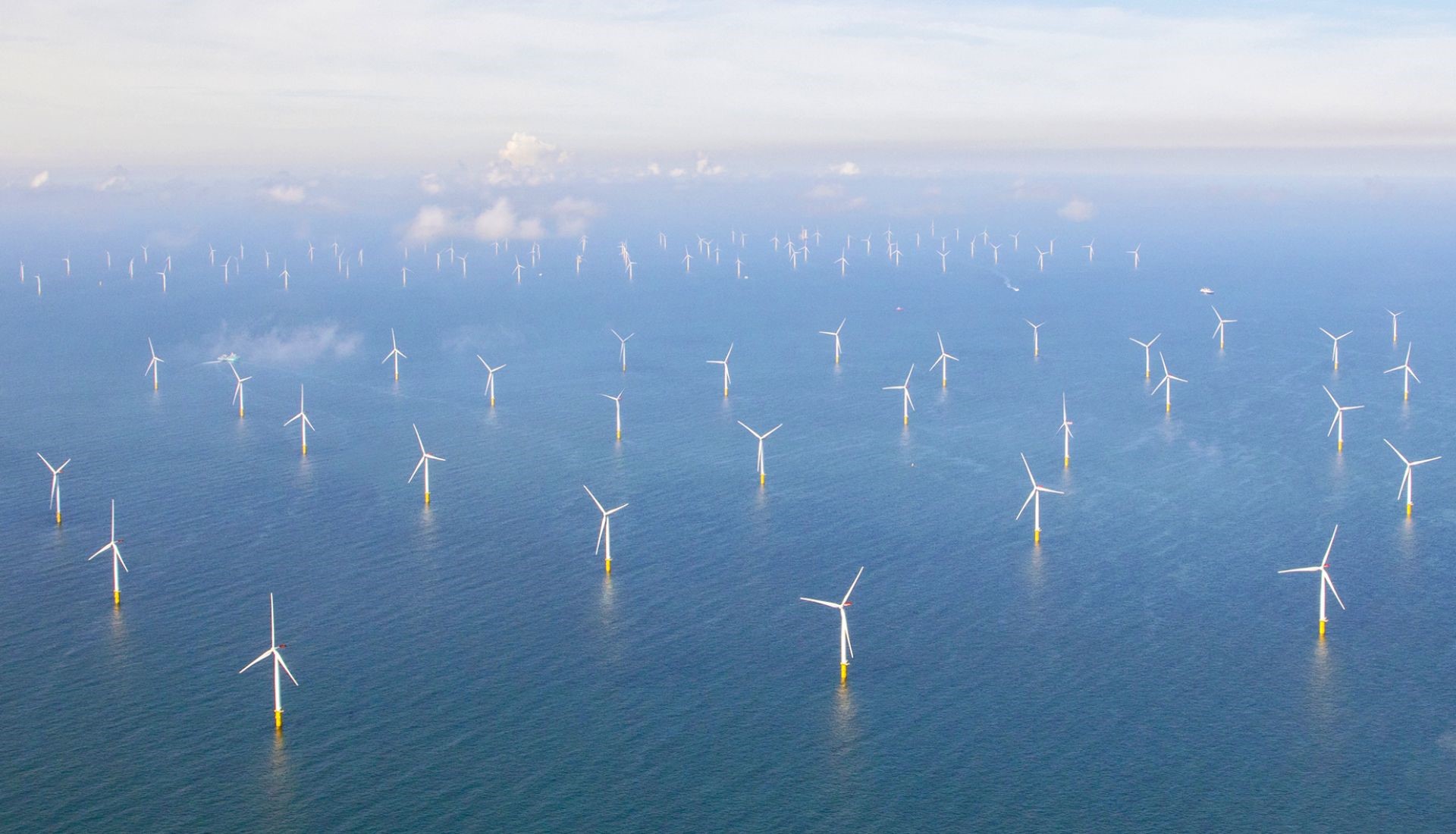
Shaping the future hydrogen economy
The big step forward will be when hydrogen can be produced on a large scale from sustainable energy - green hydrogen. Dutch industry in the TopDutch region is working hard to scale up the technology. Various research projects are underway. Multinationals such as Shell and Nouryon and energy companies such as Gasunie, RWE, Engie and Nuon form consortia with various knowledge institutions. Hydrogen is produced through electrolysis. ‘With the aid of electricity, water is split via an electrolyzer into oxygen and hydrogen’, explains Erik Heeres, professor of chemical technology at the University of Groningen. Professor Heeres is involved in Hydrohub, a test center shortly due to be opened, where an electrolyzer with a capacity of 1 megawatt will run. The partners of the project, in which approximately 6 million euros will be invested, are: Shell, TNO, Frames, Nouryon, Groningen Seaports, Hanze University of Applied Sciences, the University of Groningen, GasUnie and the research institute for process technology ISPT.
There is enough knowledge available to improve and scale up these electrolyzers.
Prof. dr. ir. H.J (Hero Jan) Heeres
According to Erik Heeres, the Netherlands has plenty of opportunities to take a leading position in the production of electrolyzers. ‘There is enough knowledge available to improve and scale up these electrolyzers.’ Hydrogen plants will certainly start operating in the North of the Netherlands in the future. In the North, large amounts of wind energy come ashore from the sea, which can be converted into hydrogen.
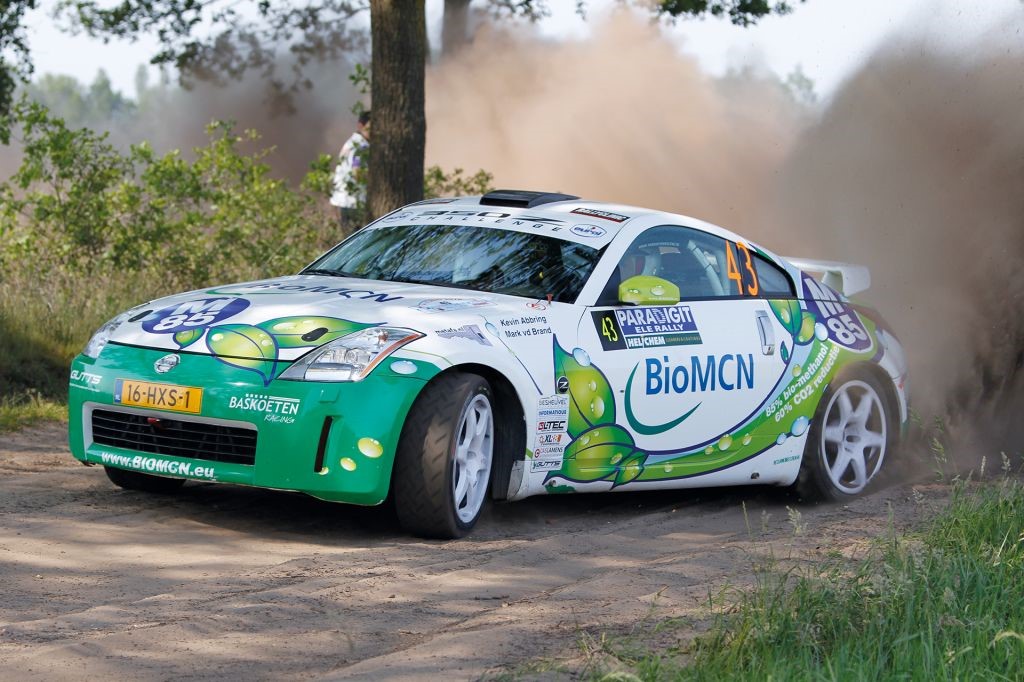
Hydrogen takes the greening of chemistry a step closer. In the future, chemical processes that still require fossil resources could partially run on hydrogen. The Groningen-based company BioMCN is a case in point. This company currently produces methanol from natural gas and biogas, but also has plans to produce methanol by having hydrogen react with CO2. This is making the company’s methanol greener and greener. In the longer term, there will be a great opportunity to supply green hydrogen via a shared infrastructure, so that all companies in the chemical cluster can benefit.
The topdutch region gaining momentum
The chemical industry needs green building blocks. This calls not only for pilot plants, but also for sustainable total solutions, an infrastructure and logistics, and a culture of intensive cooperation. Such innovations are gaining momentum in the TopDutch region. Working together, these innovative pioneers will help the chemical cluster in the Northern Netherlands to achieve its ambition of producing sustainably and CO2 negatively by 2050. ‘Developments could rapidly gain momentum’, predicts biotech professor Euverink. ‘Certainly as oil and natural gas become scarce or when governments start putting a price on CO2 emissions. Companies would do well to prepare for greener business operations.’